วาล์วควบคุมกับระบบมาตรวัดปริมาตรของเหลว
(Control Valves in Dynamic Measuring Systems)
ตอนที่ 1 บททั่วไป
ในกระบวนการผลิตในภาคอุตสาหกรรมเพื่อทำการผลิตภัณฑ์ออกสู่ตลาดนั้น อาจประกอบด้วยจำนวนกระบวนการผลิตขั้นตอนย่อยๆ ตั้งแต่หลักหน่วยจนถึงหลักพัน ซึ่งในแต่กระบวนการผลิตขั้นตอนย่อยๆดังกล่าวจะถูกออกแบบเพื่อควบคุมปัจจัยในกระบวนการผลิตที่สำคัญๆ เช่น อุณหภูมิ ความดัน อัตราการไหล ระดับความสูงของเหลวภายในถังเก็บ เป็นต้น เพื่อให้แน่ใจว่ากระบวนการผลิตย่อยๆในแต่ละวงจรนั้นๆ ได้ทำการควบคุมปัจจัยในกระบวนการผลิตนั้นๆ และเมื่อสิ้นสุดกระบวนการผลิตๆย่อยแต่ละกระบวนการรวมกันแล้วจะให้ผลผลิตภัณฑ์ที่มีคุณสมบัติตามที่ต้องการ
วาล์วควบคุมหรือ Control Valve จึงเป็นอุปกรณ์หนึ่งในหลายอุปกรณ์ในกระบวนการควบคุมกระบวนการผลิตที่เป็นที่รู้จักกันมากชิ้นหนึ่ง วาล์วควบคุมมีหน้าที่จัดการการไหลของไหล (ของเหลว + ก๊าซ) ภายในกระบวนการผลิต เช่น ไอน้ำ น้ำมันดิบ น้ำมันสำเร็จรูป ก๊าซปิโตรเลียมเหลว ก๊าซธรรมชาติ เป็นต้น เพื่อปรับ รักษาและชดเชยภาระงานของกระบวนการผลิตนั้นๆ อีกทั้งช่วยรักษาระดับค่าตัวแปรที่สำคัญและมีผลต่อกระบวนการผลิตในระบบควบคุมให้มีค่าตัวแปรในกระบวนการผลิตใกล้เคียงกับค่าที่ต้องการ (set point)
วาล์วควบคุมหรือ Control Valve หมายถึง อุปกรณ์ที่ถูกขับเคลื่อนด้วยกำลังจากภายนอกเพื่อปรับเปลี่ยนอัตราการไหลของของไหลในระบบการควบคุมกระบวนการทำงานหนึ่ง วาล์วควบคุมจึงประกอบด้วย ตัววาล์วและอุปกรณ์เชื่อมต่อก้านลิ้นวาล์วกับกลไกการกระตุ้น (Actuator Mechanism) สามารถเปลี่ยนแปลงตำแหน่งของชิ้นส่วนควบคุมการไหล (flow controlling element) ภายในตัววาล์วหรือตำแหน่งของลิ้นวาล์วตามสัญญาณที่ได้รับจากระบบควบคุม (Controlling System) โดยไม่รวมถึง Regulator, Relief valve และ Hand Valve ดังนั้นวาล์วควบคุมจึงประกอบ 3 ส่วนหลัก คือ
1. วาล์ว (Valve) ส่วนทำหน้าที่ควบคุมการไหลของไหล ประกอบด้วย ชุดรองรับของไหล (Fluid Retaining Assembly) หรือตัวเรือนวาล์ว (Valve Body) รวมถึง ช่องทางไหล (Port) ระหว่าง Seat กับ “Flow Control Element” (หรือ “Moveable Closure Member” หรือ “ลิ้นวาล์ว”) ซึ่งเคลื่อนที่เพื่อเปิดเต็มที่ เปิดบางส่วน (Restricts) หรือปิดช่องทางไหลนั้น (ในเอกสารบางฉบับเรียก Seat กับ ลิ้นวาล์วรวมๆ กันว่า Trim) ทั้งนี้ช่องทางไหลภายในตัวเรือนวาล์วอาจมีมากว่า 1 ช่องทางไหล ดังนั้นจึงดูเหมือนเป็นองค์ประกอบพื้นฐานเช่นเดียวกับวาล์วที่ใช้มือหมุนทั่วๆไป (Hand Valve หรือ Manual Valves) ซึ่งเป็นชนิดของวาล์วที่ไม่สามารถควบคุมได้ด้วยตัวมันเองต้องอาศัยคนในการเปิด-ปิด การแบ่งชนิดประเภทของวาล์วแบ่งออกเป็นชนิดตามรูปที่ 2
2. Actuator คือ ส่วนที่ถูกขับด้วยพลังงานไฟฟ้าหรือพลังงาน ไฮดรอลิค จากนั้นทำหน้าที่แปลงพลังงานดังกล่าวให้อยู่ในรูปของงาน/แรงเชิงกลไปขับชิ้นส่วนที่ต้องการให้เคลื่อนที่ในที่นี้ก็คือ Flow Control Element หรือลิ้นวาล์ว ในบางครั้งเราอาจเรียก “Actuator” ว่า “หัวขับวาล์ว”
3. Motion conversion mechanism หมายถึงกลไกเชื่อมต่อระหว่างวาล์วกับ Actuator ซึ่งทำหน้าที่แปลงการเคลื่อนที่เชิงเส้น (Linear Motion) ไปเป็นการเคลื่อนที่เชิงมุม (Rotary Motion) นั้นคือการเปลี่ยนแปลงจากการเคลื่อนที่เชิงเส้นของ Actuator ไปเป็นการเคลื่อนที่การหมุนของลิ้นวาล์ว (Rotary Valve Operation) หรือในทางกลับกัน เปลี่ยนแปลงการเคลื่อนที่เชิงมุมของ Actuator ไปเป็นการเคลื่อนที่แนวเส้นตรงของลิ้นวาล์ว (Linear Valve Operation)
4. Accessories แต่ในบางครั้งอาจมีการเพิ่มส่วนประกอบปลีกย่อยร่วมเข้ามาเพื่อสะดวกต่อการทำงานซึ่งจะรวมไปถึงพวก Positioners, I/P Transducers, Limit Switches, Handwheels, Air Set, Position Sensor, Solenoid Valve, Travel Stops เป็นต้น
การแบ่งกลุ่มของวาล์ว
เพื่อให้เรามองภาพรวมของวาล์วควบคุมถูกวางไว้ในตำแหน่งใดในสาระบท ให้ดูรูปที่ 1 แสดงถึงการแบ่งชนิดของวาล์ว คือ
1. Hand Valve หรือ Manual Valves เป็นวาล์วที่ไม่สามารถควบคุมได้ด้วยตัวมันเองต้องอาศัยคนในการปิด-เปิดวาล์ว
2. Power Valve เป็นวาล์วที่ใช้กำลังงานจากภายนอกเป็นตัวปิด-เปิดวาล์ว เช่น พลังงานไฟฟ้า พลังงานของไหล เป็นต้น ได้มีการแบ่งย่อยลงไปเป็น
2.1. Positioning
2.1.1. Control Valve วาล์วควบคุมที่เราให้ความสนใจต่อไป ณ บัดnow
2.1.2. Regulator เป็นวาล์วที่สามารถควบคุมปริมาณหรือระยะการปิด-เปิดด้วยการตั้งค่าล่วงหน้าที่ต้องการเพื่อควบคุมตัววาล์วด้วยค่าคงที่ค่าหนึ่ง ซึ่งส่วนใหญ่ที่พบจะเป็นการตั้งค่าสปริง ยังเป็นที่ถกเถียงกันว่าในบางสถานะการณ์สามารถประหยัดเงินได้มากหากเราใช้ Regulator แทน Control Valve ซึ่งเป็นเรื่องน่าคิดเช่นกัน แต่ต้องรู้จริงก่อนตัดสินใจ
2.2. Stop Valve or Block Valve ก็มึนๆ เหมือนกันไม่รู้จะอธิบายง่ายๆ อย่างไร เอาเป็นอย่างนี้ว่าถ้าระบบท่อต้องการติดตั้งวาล์วเพื่อให้มันเปิดอย่างเดียวอย่างนี้มันก็ไม่ต้องติดตั้งเสียเวลาและเสียเงินทอง ดังนั้นที่ต้องการติดตั้งวาล์วในระบบเพราะต้องการมันทำหน้าที่ปิดหรือสกัดของไหลภายในท่อไม่ให้ไหลผ่านในเวลาที่ต้องการหรือเมื่อต้องการตัดระบบแยกออกไปเพื่อทำการซ่อมแซมในระบบอื่นๆที่ติดกัน ฝรั่งเลยเรียก Stop Valve ผมก็ยังสงสัยว่าทำไมไม่เรียก Open Valve บ้างละ แล้ว On/Off หรือ Starting/Stopping หากพูดไม่ต้องคิดมากก็คือวาล์วที่ใช้มีหน้าที่ 2 อย่างคือ ปิดและเปิด ส่วนภาษาก็ว่ากันนะหากมีข้อมูลใหม่ก็บอกด้วย ผมติดหล่มความคิดครับ!!
2.3. Relief Valve วาล์วทำหน้าที่ระบายความดัน หรืออุณฆภูมิภายในระบบ
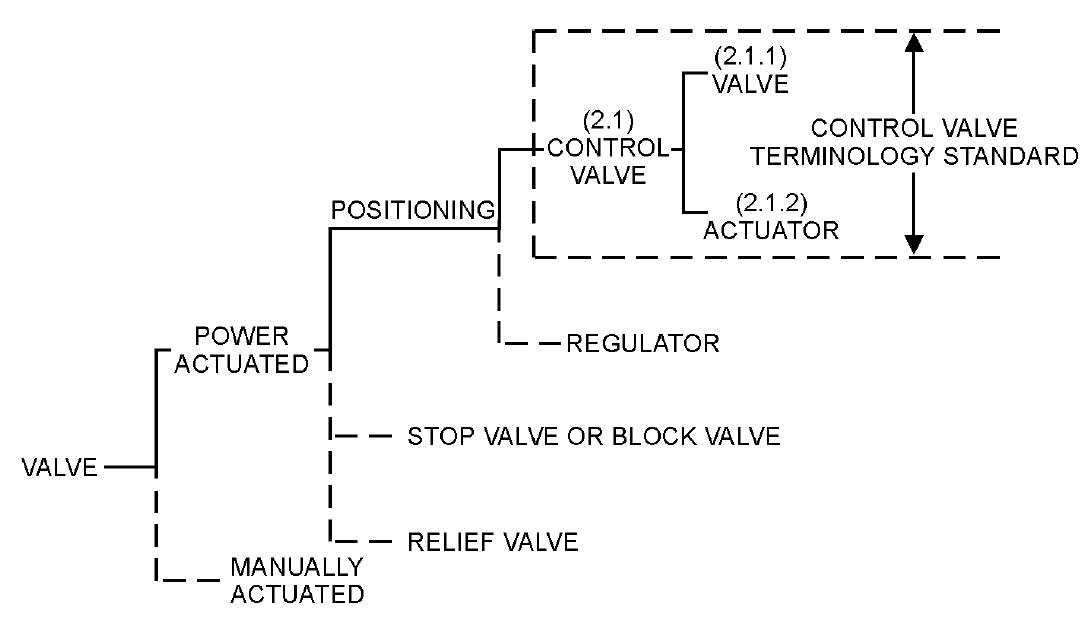
รูปที่ 1 การแบ่งกลุ่มวาล์ว ตาม ISA-S75.05-1983
แต่ก่อนที่เราจะมึนเพราะมีวาล์วมากมายหลากหลายชนิดที่ถูกออกแบบมาเพื่อแก้ไขปัญหาชีวิตของแต่กระบวนการหนึ่ง ดังนั้นเพื่อลดปัญหากวนใจและจำกัดขอบเขตเนื้อหาในตอนนี้และในตอนต่อๆไป (เรื่องมันเยอะต้องแบ่งตอน เหมือนแต่งนิยาย..สร้างมูลค่าเพิ่ม) เราจึงสนใจเฉพาะวาล์วควบคุมเท่านั้นเพราะมันกระทบต่อการทำงานชั่งตวงวัดตามข้อกำหนดของกฎหมาย เรามาดูรูปที่ 2 ซึ่งแบ่งวาล์วควบคุม (Control Valve) ออกเป็น
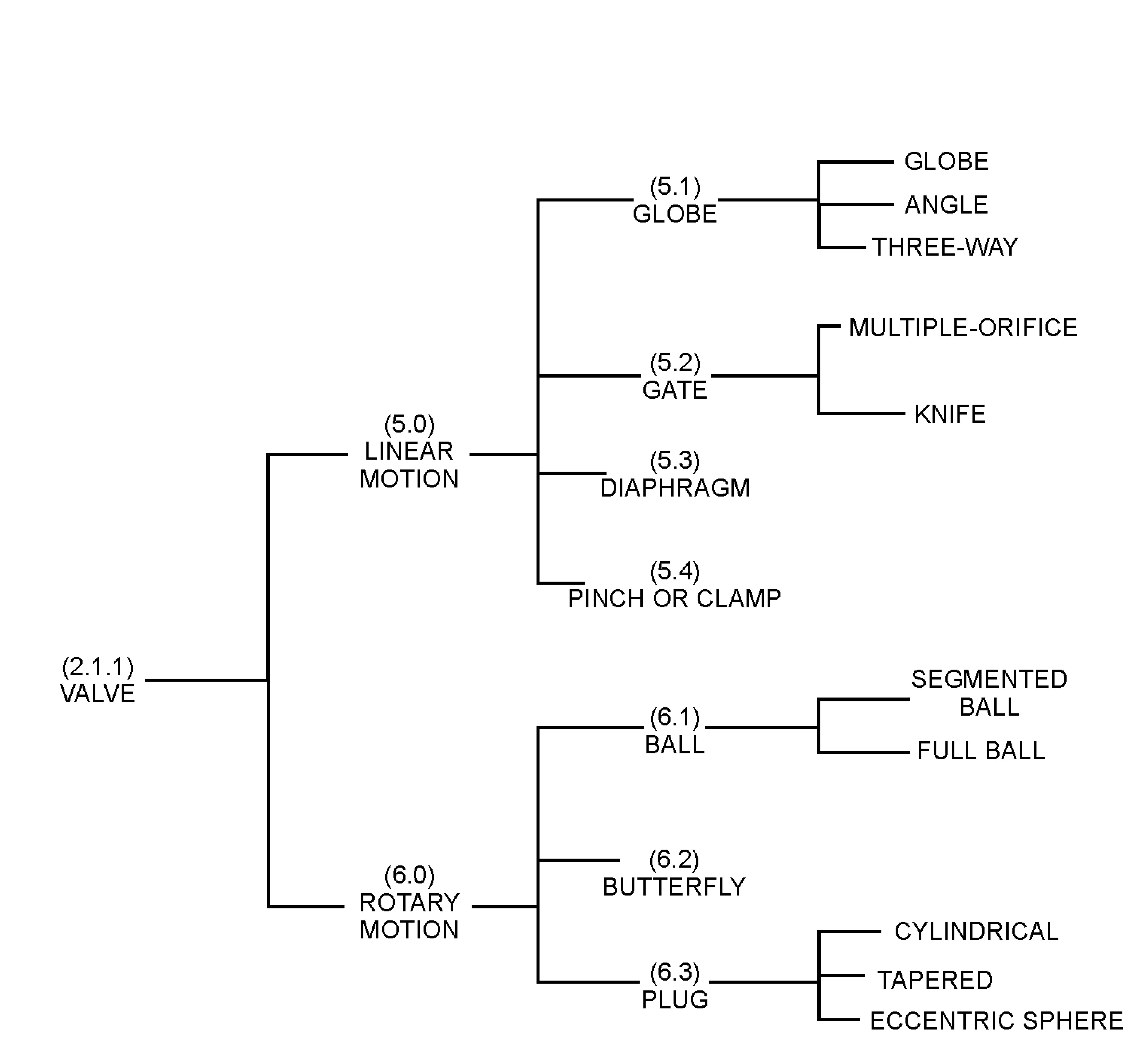
รูปที่ 2 การแบ่งกลุ่มวาล์วควบคุม ตาม ISA-S75.05-1983
1. Linear Motion ลักษณะการเคลื่อนที่ของก้านวาล์วซึ่งต่อเชื่อมไปยังลิ้นวาล์วเป็นเส้นตรง อาจเป็นแนวดิ่งหรือแนวเอียงก็ได้เมื่อทำการปิด หรี่ หรือเปิดวาล์วสุด เป็นการออกแบบที่ง่ายและสะดวกต่อการบำรุงรักษา สามารถผลิตได้หลากหลายขนาดที่ความดันใช้งานและอุณหภูมิที่แตกต่างกัน ได้แก่
1.1. Globe Valve
1.2. Gate Valve
1.3. Diaphragm Valve
1.4. Pinch or Clamp Valve
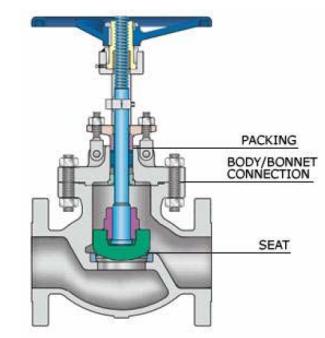
รูปที่ 3 Linear Motion
2. Rotary Motion ลักษณะการเคลื่อนที่ของก้านวาล์วซึ่งต่อเชื่อมไปยังลิ้นวาล์วเป็นการหมุนของก้านวาล์วเพียง 90 องศา ทำให้ลิ้นวาล์วมีลักษณะเคลื่อนที่หมุนเข้าและหมุนออกเพื่อปิดหรือเปิดช่องทางการไหลภายในวาล์วเมื่อทำการปิด หรี่หรือเปิดวาล์วสุด ส่งผลให้วาล์วซึ่งมีหลักการทำงานชนิดนี้จึงมีขนาดช่องทางการไหล (port) ใหญ่กว่า แต่มีขนาดและน้ำหนักวาล์วน้อยกว่าวาล์วแบบ Linear Motion แต่ในขณะเดียวกันวาล์วชนิดนี้มีความดันตกคร่อมที่มากกว่าวาล์วแบบ Linear Motion ปัจจัยนี้เองจึงเป็นข้อจำกัดที่สำคัญในการเลือกใช้งาน ได้แก่
2.1. Ball Valve
2.2. Butterfly Valve
2.3. Plug Valve
รายละเอียดของวาล์วแต่ละชนิดจะอธิบายในตอนถัดไปข้างหน้าใจเย็นๆ....
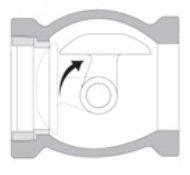
รูปที่ 4 Rotary Motion
เนื่องจากวาล์วถูกเลือกใช้งานในขอบเขตที่กว้างขวาง ทำให้ในบางครั้งก็มีการจัดกลุ่มชนิดของวาล์วที่แตกต่างกันออกไปจากรูปที่ 2 เช่น
ก. แบ่งชนิดของวาล์วตามการใช้งาน (Application) ก็สามารถแบ่งได้ว่า
· General Service การใช้งานทั่วไป เช่นความดันภายในระบบท่อไม่สูงมากนักอยู่ในช่วง 150-600 Psig อุณหภูมิอยู่ในช่วง -45 – 340 °C เป็นของไหลกัดกร่อนต่ำ เป็นต้น
· Special Service การใช้งานเฉพาะทางหรือออกแบบเป็นกรณีพิเศษด้วยเงื่อนไขไม่ปรกติ เช่น ความดันสูงมากเป็นพิเศษ ของไหลในระบบท่อมีความเป็นกรดด่างสูงมาก หรือต้องการวัสดุพิเศษ เป็นต้น
· Severe Service เป็นวาล์วที่ถูกใช้งานในสภาพแวดล้อมและสภาวะกระบวนการทำงานที่รุนแรงอย่างยิ่งยวด (Critical Process) เช่น การไหลในระบบท่อมีความดันตกคร่อมสูงมากๆ (คือความดันทางเข้าวาล์วสูงมากๆ แล้วเมื่อผ่านวาล์วควบคุม เราต้องการให้ความดันด้านออกวาล์วควบคุมมีค่าความดันต่ำมากเพื่อให้ของไหลมีความดันเหมาะกับกระบวนการทำงานนั้นๆ) ซึ่งอาจเกิดจาก Cavitation, Flashing, Choking, หรือในระบบท่อที่มีเสียงดังในระดับสูง, ในสภาวะอุณหภูมิร้อนจัดหรือเย็นจัด, ของไหลมีความเป็นกรดด่างเข้มข้นสูง เป็นต้น
โดยปรกติทั่วไปวาล์วที่ใช้งานในกระบวนการหนึ่งจะมีความแตกต่างของความดันสูงฝั่งขาเข้าวาล์ว (Upstream) P1 เทียบกับความดันต่ำฝั่งขาออกวาล์ว (Downsteam). P2 ไม่ควรมีค่าเกิน 50% (P1-P2 < 50%) แต่ถ้าหากค่าความแตกต่างของความดันมีค่าสูงมากกว่านี้เราจะเรียกว่า “High Pressure Drop Valves” หรือ “Severe Service Valve” ในสภาวะค่าความแตกต่างของความดันมีค่าสูงภายในตัววาล์วเช่นนี้ชิ้นส่วนภายในตัววาล์วจึงต้องรองรับพลังงานอันมหาศาล (จากความแตกต่างของความดันสูงระหว่างขาเข้า-ขาออกวาล์ว) จากหลักการพลศาสตร์ของไหล (Fluid Dynamic) เมื่อของไหลที่มีความดันสูงถูกบังคับให้วิ่งผ่านพื้นที่แคบลง ความดันจะขับเคลื่อนของไหลให้เคลื่อนที่เร็วสูงขึ้นอย่างมากหรือเปลี่ยนแปลงรูปแบบพลังงานเนื่องจากความดันกระทำต่อของไหลไปเป็นรูปแบบพลังงานจลน์ (Kinetic energy) นั้นเอง และเจ้าตัวความเร็วของของไหลนี้เองที่เป็นสาเหตุทำให้เกิดความเสียหายรวมทั้งเกิดการกัดกร่อนเชิงกล (Erosion) แก่ชิ้นส่วนภายในของตัววาล์วชนิด “Severe Service Valve”
ข. แบ่งกลุ่มหรือชนิดของวาล์วตามหน้าที่การทำงาน (Function) ก็สามารถแบ่งย่อยเป็น
· On/Off ในบางครั้งอาจเรียกว่า “Block Valve” ใช้งานสำหรับเริ่มต้นและสิ้นสุดหยุดส่งจ่ายของไหลเข้ากระบวนการขั้นตอนใดขั้นตอนหนึ่ง ส่วนใหญ่จะเป็นวาล์วที่ปิด-เปิดด้วยคน เช่น Gate Valve, Plug Valve, Ball Valve, Pressure Relief เป็นต้น หรืออาจเรียก Stop Valve ด้วยกระมัง
· Non-Return วาล์วทำหน้าที่ควบคุมทิศทางการไหลให้ไปในเฉพาะทิศทางที่ต้องการทุกๆอัตราการไหลและทุกความดันขณะทำงาน อาจด้วยเหตุผลเช่นเพื่อป้องกันความเสียหายที่อาจก่อให้เกิดกับอุปกรณ์ต้นทาง เป็นต้น ตัวอย่างเช่น Check Valve
· Throttling วาล์วสำหรับควบคุมการไหล อุณหภูมิ หรือความดันในระบบท่อ ลิ้นวาล์วสามารถเคลื่อนที่ขึ้นลงหรือหมุนปิดเปิดช่องทางไหลภายในตัววาล์วได้ทุกระดับ ซึ่งส่วนใหญ่จะประกอบด้วย Actuator เพื่อควบคุมระดับการปิดเปิดของวาล์ว ได้แก่ วาล์วควบคุม และ Pressure Regulator
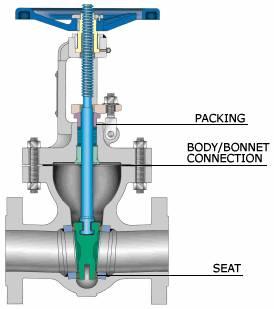
รูปที่ 5 On/Off หรือ Block Valve
|
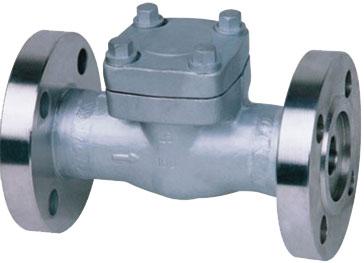
รูปที่ 6 Non-Return Valve
|
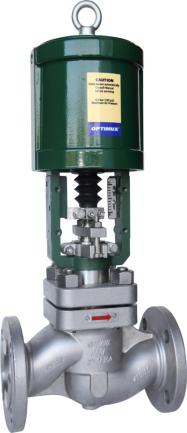
วาล์วควบคุม
|
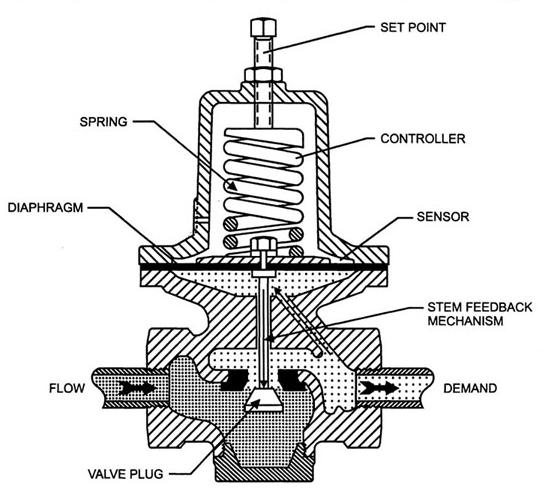
Regulator
|
รูปที่ 7 Throttling Valve
· Final Control Element ในกระบวนการผลิตแต่ละกระบวนการที่มีระบบควบคุมการทำงานใดๆ (ดูรูปที่ 8) ก็ตามจะประกอบด้วยตัวตรวจจับ (sensors) เพื่อตรวจจับสภาวะเงื่อนไขของกระบวนการทำงานระบบนั้นๆ จากนั้นค่าที่วัดได้จากตัวตรวจจับก็จะถูกแปลงค่าให้เหมาะสมกับระบบควบคุมโดยตัวถ่ายทอดสัญญาณ (Transmitter) และถูกส่งค่าออกไปยังตัวควบคุมประมวลผล (Controller) จากนั้นตัวควบคุมประมวลผลทำการเปรียบเทียบระหว่างค่าที่ต้องการหรือตั้งค่าไว้ (Set Point) กับค่าที่ได้รับจากตัวตรวจจับที่ส่งข้อมูลผ่านมาโดยตัวถ่ายทอดสัญญาณ เมื่อได้ผลการเปรียบเทียบเป็นอย่างไรตัวควบคุมจะแปลงความหมายแล้วส่งสัญญาณปรับค่าแก้ไขกลับไปยัง “Final Control Element” ในกระบวนการทำงานของระบบ ซึ่งเป็นส่วนปลายสุดของระบบควบคุมของกระบวนการทำงานดังกล่าว...นั้นก็คือ..วาล์วนั้นเอง (เฉพาะเนื้อหาในที่นี้) ด้วยเหตุนี้วาล์วจึงต้องการพลังงานจากภายนอกเพื่อใช้ในการทำงาน
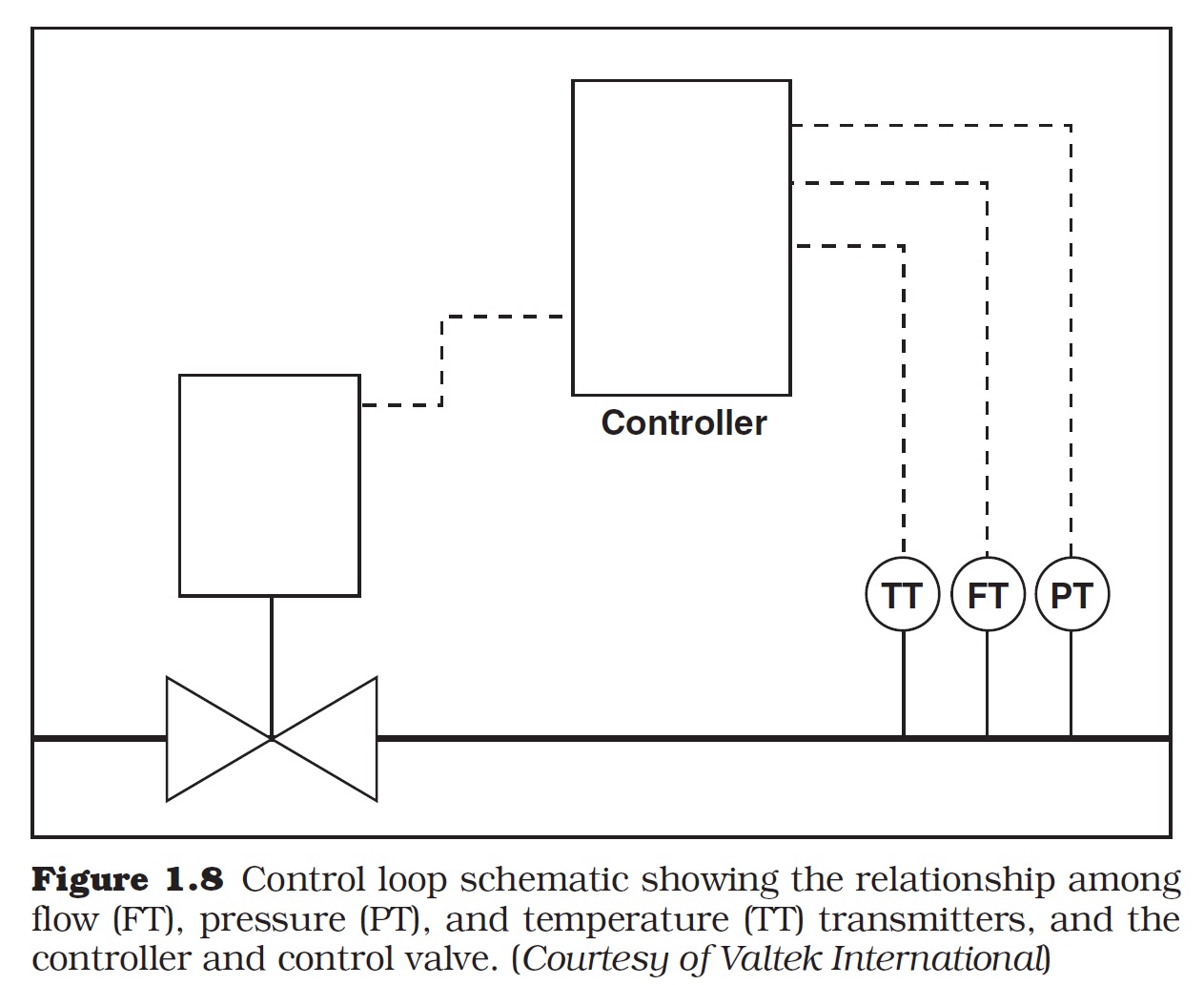
รูปที่ 8 Final Control Element
วาล์วควบคุมมีผลต่อระบบควบคุมวงรอบปิด (Process Control Loop) อย่างไร
เรามาดูรูปที่ 9 ซึ่งแสดงการควบคุมวงรอบปิด (Process control loop) เพื่อมาดูว่าวาล์วควบคุมทำอะไรในกระบวนการทำงานหนึ่งๆ จะเห็นได้ว่ามี 3 หน้าที่สำคัญหลัก (Function Blocks) คือ
1. Control Valve Gain (Kv) ค่านี้สามารถหาได้จาก “Installed Flow Characteristic” ของวาล์วภายหลังจากถูกตั้งเข้ากระบวนการทำงาน ซึ่งค่านี้จะแตกต่างจากค่าที่ปรากฏในแค็ทตาล็อกของวาล์วที่ผู้ขายส่งมอบ ค่า Kv บอกให้เราทราบว่าการไหลของไหลผ่านวาล์วมีการเปลี่ยนแปลงปริมาณเท่าไรต่อการเปลี่ยนแปลงสัญญาณที่วัดได้ เช่น สัญญาณไฟฟ้ามาตรฐาน 4-20 mA สัญญาณแรงดันลม 3-15 psi
โดยทั่วไปแล้วตัวถ่ายทอดสัญญาณ (Transmitter) เป็นอุปกรณ์ที่ทำหน้าที่แปลงสัญญาณทางไฟฟ้าทางด้านเอาต์พุตที่ได้จากตัวตรวจจับ (sensor) หรือทรานสดิวเซอร์ (Transducer) ให้เป็นสัญญาณมาตรฐานเพื่อใช้พูดคุยสื่อสารกับอุปกรณ์ต่างๆในระบบที่ทำงานร่วมกัน แบ่งออกเป็น 2 ประเภทได้แก่ สัญญาณนิวแมติกส์และสัญญาณทางไฟฟ้า
· สัญญาณนิวแมติกส์ (Pneumatics Signal) เป็นสัญญาณมาตรฐานที่อยู่ในรูปของความดันลม ใช้ความดันของลมในการควบคุมกระบวนการ ตัวอย่างสัญญาณมาตรฐานนิวแมติกส์ ได้แก่ 3-15 psi (BS), 0.2-1 bar (Metric) และ 0.2-1 kg/cm2 (Metric)
· สัญญาณทางไฟฟ้า (Electrical Signal) เป็นสัญญาณมาตรฐานที่อยู่ในรูปของแรงดันไฟฟ้าและกระแสไฟฟ้าแบ่งออกเป็น 2 แบบ แบบแรก คือแรงดันไฟฟ้า 1-5 V กระแสไฟฟ้า 4-20 mA และแบบหลังคือแรงดันไฟฟ้า 0-10 V กระแสไฟฟ้า 0-100 mA
.jpg)
รูปที่ 9 Schematic block diagram of controller, control valve, and process in a control loop.
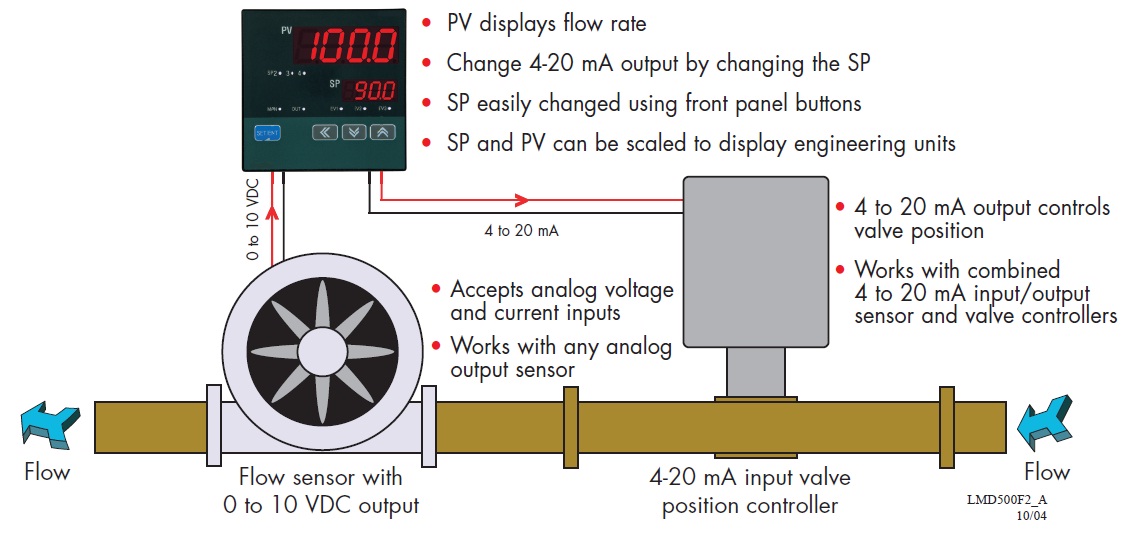
รูปที่ 10 ตัวอย่าง Flow Control ด้วย Digital Controller
2. Control Valve Deadtime (TDv) บ่งบอกระยะเวลาที่เสียไปสำหรับ Actuator (เช่น Pneumatic Actuator) ในการปรับเปลี่ยนความดันเพื่อไปหมุนปรับระยะปิด-เปิดของวาล์ว ก่อนวาล์วเคลื่อนที่เพื่อให้เป็นไปตามปริมาณสัญญาณที่ถูกส่งมาจากตัวควบคุม (Controller) ซึ่งค่าระยะเวลาที่เสียไปดังกล่าวนี้จะขึ้นกับตัววาล์วและความฝืดในการทำงานของ actuator แต่ไม่รวมระยะเวลาที่สูญเสียไปกับเวลาหน่วงของการถ่ายทอดแรงดันลมของตัวถ่ายทอดสัญญาณและระยะเวลาในการสร้างแรงดันในตัวเรือน Diaphragm ของ Actuator (ตัวอย่างในกรณีที่เป็น Diaphragm Actuator) ค่า Control Valve Deadtime จึงมีความสัมพันธ์ที่ใกล้ชิดกับค่า Dead Band ของการทำงานร่วมกันของวาล์วและ Actuator ซึ่งค่า Dead Band ดังกล่าวนี้เองทำให้วาล์วไม่สามารถตอบสนองทันทีทันใดเมื่อได้รับสัญญาณที่เปลี่ยนแปลงจากตัวควบบคุม ส่งผลต่อเนื่องก่อให้เกิด Control Valve Deadtime โดยทั่วไปแล้วค่า Dead Band ของวาล์วจะมีค่าไม่เกิน 5% ของช่วงสัญญาณมาตรฐาน นั้นคือมีค่าน้อยกว่า 0.6 psi (12*5/100 = 0.6) ของช่วงสัญญาณนิวแมติกส์มาตรฐาน 3-15 psi หรือ 0.8 mA ของช่วงสัญญาณกระแสไฟฟ้ามาตรฐาน 4-20 mA
แต่ในกรณีทำงานร่วมกันของวาล์วและ Positioner (ดูรูปที่ 11) โดยทั่วไปแล้วค่า Dead Band ของวาล์วจะมีค่าไม่เกิน 0.5% ของช่วงสัญญาณมาตรฐาน นั้นหมายถึงการติดตั้ง Positioner ประจำวาล์วควบคุมสามารถช่วยลด Dead Band ได้อย่างน่าพอใจ
สำหรับวาล์วที่มีปะเก็นอัดแน่นรอบก้านวาล์ว (Tight stem packing) ในทางอุดมคติแล้วควรมีค่า operating dead band น้อยกว่า 1% ของช่วงสัญญาณมาตรฐาน
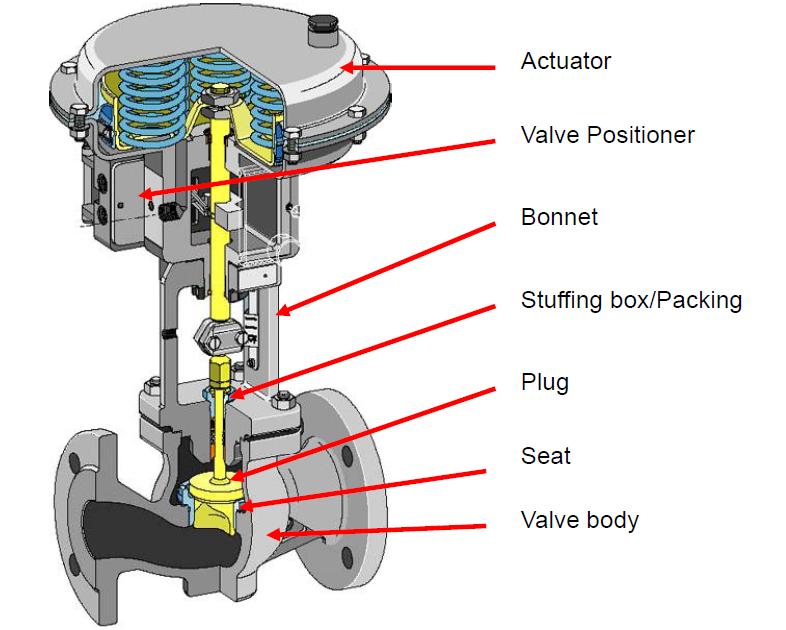
รูปที่ 11 Final Control Element
3. Control Valve Time Constant (TCv) ค่านี้เปรียบเสมือนความเร็วของช่วงชักหรือช่วงการหมุนของก้าน Actuator หรือความเร็วของ Actuator กับ Positioner รวมกัน นั้นคือความเร็วของวาล์วในการตอบสนองต่อค่าสัญญาณที่ส่งมาจาก controller สั่งให้ปรับเปลี่ยนตำแหน่งปิดเปิดวาล์วในเทอมของ Actuator ดังนั้นจึงเป็นเวลาที่เสียไปจากผลการทำงานร่วมกันของ Actuator กับ Positioner
สำหรับวาล์วควบคุมในอุดมคติแล้วควรเป็นวาล์วมีค่า Control Valve Gain (Kv) คงที่ตลอดช่วงอัตราการไหลนั้นคือมีคุณลักษณะของทำงานที่เรียกว่า Linear “installed” flow characteristic และต้องมีค่า Control Valve Deadtime (TDv) ภายใต้เงื่อนไขวาล์วที่มีปะเก็นอัดแน่นของก้านวาล์ว (Tight stem packing) เท่ากับ 0 สุดท้ายต้องมี Control Valve Time Constant (TCv) ต่างจาก Process Time Constant อย่างน้อย Factor of 3 (ผมยอมรับว่ายังหาคำตอย ว่าเลข 3 หมายถึงอะไร ค่อยๆคิดด้วยกันนะครับ ??????)
ชั่งตวงวัด; GOM MOC
นนทบุรี
20 ก.ย.60